钛合金与镍钛合金:重塑机器人的 “钢铁之躯”
人形机器人正从塑料轻量化转向金属功能化。传统 PEEK 材料(拉伸强度 100MPa)难以满足高动态负载需求,钛合金与镍钛合金的突破重塑关节性能:
钛合金复合结构:通过钛合金 - 碳纤维叠层技术,关节扭矩密度达 450Nm/kg,重量减半,刚度提升 3 倍,支持 - 50℃至 150℃极端环境作业,工业级搬运负载能力突破 50 公斤。
镍钛形状记忆合金:0.5mm 细丝束实现 10 公斤夹持力,能耗降低 90%,-50℃至 150℃范围内完全形状回复,应用于精密抓取系统,触觉精度达 0.1N/mm²,可稳定操作毫米级物件。
稀土永磁:电机驱动的 “隐形心脏”
伺服电机作为机器人 “心脏”,依赖高性能钕铁硼磁材实现能效突破:
单台机器人需 40 + 伺服电机,消耗 2-4 公斤钕铁硼,用量为新能源车的 1.7 倍。2025 年全球高性能钕铁硼需求预计 13 万吨,机器人领域贡献近 3% 增量。材料磁能积突破 55MGOe,推动电机效率提升至 97%,体积缩小 40%,支撑复杂动作的精准控制。
液态金属:从科幻到现实的颠覆性突破
镓基合金突破固态限制,开启柔性机械时代:
磁控相变技术实现常温固液转换,负载能力 30 公斤,响应速度 1.5m/s,已应用于医疗介入机器人,可通过人体狭窄腔道完成毫米级操作。
液态金属轴承使关节摩擦系数降至 0.001,寿命延长 5 倍,适配极端粉尘、高低温环境,预计 2030 年后在工业维护、深海作业场景规模化应用。
产业影响与未来图景
成本与效率重构:金属基材料使机器人负载 / 自重比提升 200%,单台制造成本下降 40%,推动工业场景渗透率从 15% 向 40% 跨越。
应用边界拓展:耐低温镍钛合金支持极地科考机器人,液态金属组件解锁太空微重力环境作业,医疗机器人操作精度进入亚毫米级时代。
供应链博弈:中国控制全球 70% 稀土产量,在钕铁硼烧结技术保持领先;美欧加速布局替代材料,推动深海采矿与再生稀土技术研发,全球材料竞争进入 “性能 + 地缘” 双赛道。
风险与技术路径
替代威胁:碳纳米管材料理论强度达 1TPa,可能颠覆传统合金体系;韩国三星 SDI 等启动碳基电机研发,目标 2028 年实现商业化。
伦理挑战:高灵敏度触觉反馈引发人机交互伦理讨论,欧盟推动机器人触觉系统加入 “力反馈限制” 设计,防止过度拟人化风险。
这场由金属材料驱动的变革,正重新定义人形机器人的物理性能与应用场景。从刚性支撑到柔性变形,从能量转换到智能响应,材料创新不仅是技术突破,更成为产业竞争的核心壁垒。掌握核心金属材料技术的企业,将在未来十年的智能装备革命中占据战略制高点。
(以上观点仅供参考,不做为入市依据 )长江有色金属网
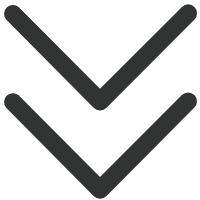